Сложившаяся ситуация в авиации России отразилась на потреблении авиационных шин. В гражданской авиации (ГА) существенно увеличилась доля импортной составляющей и снизилась – российская. Санкции затруднили обеспечение потребностей ГА в авиашинах. Сегодня импортозамещение – жизненно важная задача ГА [1]. Вместе с тем, в условиях СВО вследствие повышения интенсивности эксплуатации военной авиации (ВА), использующей отечественные шины, ежегодно увеличивается потребность в них. Один из наиболее эффективных факторов импортозамещения в ГА и удовлетворения растущих потребностей в авиашинах ВА – это организация восстановительного ремонта изношенных авиационных шин в России.
Отличительная особенность авиационных шин – дифференциация ресурсов каркаса и протектора: чрезвычайно высокий запас прочности каркаса и сравнительно не большая масса протектора, обусловленные особенностями работы шины в эксплуатации и её конструкцией. Поэтому единственный, рациональный способ их практического применения – эксплуатация с системным восстановлением изношенной беговой части протектора. Ресурс отечественных авиашин обеспечивает, по меньшей мере, 4х кратное возобновления протектора. При эксплуатации шины до износа рисунка протектора и его многократного восстановления достигается оптимальный уровень суммарной долговечности шины, экономической эффективности и безопасности их.
За рубежом накоплен большой опыт восстановления авиационных шин для гражданской и военной авиации. Впервые применять восстановленные авиационные шины стали с 1943 г. во время Второй мировой войны в ВВС США Через 20 лет в США уже было восстановлено более 1 млн. авиашин, выполнивших более 200 млн. взлёт-посадок. В мировой практике восстановленные шины используют на всех видах массовых турбовинтовых и реактивных самолётах без ограничения числа устанавливаемых восстановленных шин, как на основные, так и носовые шасси. В конце прошлого века доля восстановленных шин, эксплуатируемых мировым парком гражданской авиации, составляла 50-80%. По данным фирмы Michelin самолёты авиакомпаний, которым она поставляет шины, в настоящее время на 70% оснащены восстановленными шинами. При этом широко практикуется многократное возобновление протектора. Большой тройкой крупнейших производителей авиационных шин (компаниями Michelin, Goodyear-Dunlop, Bridgestone) создана, практически, по всему миру сеть современных предприятий по восстановлению их изношенных авиашин (~20 предприятий). Все указанные компании восстанавливают авиашины, как для гражданской авиации, так и для ВВС.
Активно развивается восстановление авиашин в Китае: открыто крупное совместное предприятие восстановления авиашин Dunlop Taikoo Aircraft Tyres Company в Цзиньцзяне. Корпорацией Bridgestone открыт новый завод по восстановлению авиационных шин в Циндао. Это пятый завод Bridgestone по восстановлению авиационных шин. Остальные расположены в Японии, США, Бельгии и Гонконге. Известны независимые от этих гигантов предприятия: компания Lanyu Aircraft в Гуинлине (мощность производства 80 000 новых авиашин и 20 000 – восстановленных) с исследовательским и испытательным центром, компания Leshan Yalun Mold Co, Ltd в Лешане по разработке и производству оборудования для восстановления авиашин. В свете современной политики развития отношений с Китайской народной республикой [1] представляет несомненный интерес широкий опыт КНР в этой области, особенно, в свете реализации решений недавнего визита председателя КНР Си Цзиньпина.
В Индии фирма Elgi Aviatioin Tyres, успешно восстанавливает авиашины, в т.ч. российские 1300х480 и 1100х330 самолётов Ил-76, Ил-78. При этом наработка восстановленных шин в эксплуатации по сообщению индийской стороны была в 1,5 раза больше новых, в т.ч. шин с повторно восстановленным протектором. Осваивают восстановление авиашин основных и носовых стоек шасси военно-транспортных самолётов Ан-32 и др. Партия шин 1300х480, эксплуатировавшихся в российских ВВС, восстановленных этой фирмой, прошла с положительным результатом стандартные для новых авиашин стендовые испытания в Ярославском центре «Вершина».
НИИ шинной промышленности (НИИШП) и Ярославским шинным заводом были выпущены опытные партии шин 930х305, 1100х330 и совместно с ГосНИИ ГА проведены всесторонние испытания восстановленных шин по программам, соответствующим ГОСТ № 15.301-80 «Постановка на производство изделий военной техники» и Квалификационным требованиям на авиашины Авиационного Регистра Международного Авиационного Комитета, в том числе: лабораторные, стендовые, специальные лётные и эксплуатационные испытания на турбовинтовых и реактивных самолётах гражданской и военной авиации дальнего действия. Показаны надёжность восстановленных авиашин, в т. ч. с повторным возобновлением их протектора при равных до- и после – ремонтных наработок.
В 80-е годы было организовано серийное производство восстановленных авиашин на Ярославском ШРЗ. Всего за 10 лет работы ЯШРЗ было восстановлено и передано в эксплуатацию более 15 тыс. авиашин 1100х330 и 930х305, в т.ч. повторно восстановленные. Случаев их отказов и претензий к качеству восстановительного ремонта не имелось. Послеремонтная наработка восстановленных шин и причины снятия их с эксплуатации были такими же, как у новых. Максимальный годовой объём производства восстановленных шин был 5000 шт. Низкий уровень объёмов восстановления авиашин в первую очередь, был связан с недостаточным количеством пригодных для восстановления шин, собираемых в авиационных предприятиях. Как правило, шины отбирали из числа, снятых с эксплуатации из-за механических повреждений и износа протектора до каркаса, исключавших возможность их дальнейшей эксплуатации и восстановления.
Несмотря на требование ТУ38.404 276-94 на авиационные шины, своевременно снимать авиашины для восстановления с износом только рисунка протектора. Основные причины этого – недостаточная культура эксплуатации и действующий регламент, допускающий эксплуатацию авиационных шин с износом протектора до корда каркаса. Во время эксплуатации шин после износа рисунка протектора вероятность механических повреждений каркаса увеличивается в 2-3 раза, поэтому при эксплуатации шины до износа только рисунка протектора и его многократным восстановлением достигаются оптимальные уровни суммарной долговечности шин, экономической эффективности и безопасности их применении.
За рубежом осуществляют своевременный строго нормированный демонтаж с самолётов авиашин (рис. 1), пригодных для восстановления протектора с износом лишь его рисунка или до индикаторов допустимого износа рисунка и со строго ограниченным размером мелких наружных повреждений каркаса, не снижающих его надёжность.
Рисунок 1. Износ рисунка протектора, с которым шину снимают с эксплуатации и оценивают её пригодность к восстановлению: а — нормальный равномерный износ центральных канавок, до 1/8 длины окружности шины (плечевые канавки могут быть видны); б — обнажение защитного (у радиальных шин) или армирующего слоёв (у диагональных шин) по месту радиального биения шины и повышенного износа по центру беговой дорожки из-за большого давления в шине в эксплуатации; в — обнажение (в левой плечевой зоне) кромки защитного или армирующего слоя, запрессованной в крупный плечевой выступ рисунка протектора в процессе вулканизации новой шины (дефект производства), не редко обнаруживаемый (даже у импортных шин) при повышенном износе плечевой зоны из-за пониженного давления в шине и нарушения углов схода и развала колёс самолёта. Шины с износом типа «б, в» требуют одновременно с восстановлением изношенного рисунка протектора возобновления повреждённых защитного и армирующих слоёв корда.
Современные авиашины, особенно, подлежащие после износа протектора восстановлению имеют, как правило, в подканавочном слое над брекером специальные армирующие слои высокопрочного текстильного корда (в шинах диагонального построения) или защитный слой металлокорда (в радиальных шинах), которые наряду с улучшением эксплуатационных качеств шин служат защитой нижележащих слоёв брекера и каркаса от механических повреждений при качении колеса по аэродромному покрытию. Вместе с тем, сами эти слои в шинах, снимаемых с эксплуатации, имеют массу мелких повреждений (и очагов коррозии металлокорда, в шинах R), поэтому наиболее существенным требованием к современному процессу восстановительного ремонта авиашин является, наряду с возобновлением изношенного протектора, – восстановление армирующих и защитных слоёв корда.
В середине 90-х годов, в НИИШ бала восстановлена опытная партия отечественных диагональных шин 930х305 с армированием протектора, проведены их всесторонние лабораторные и стендовые испытания. АНТК им. А. Н. Туполева и ГосНИИ ГА провели подконтрольную эксплуатацию этих шин на самолетах гражданской авиации, в т.ч. выполнявших регулярные перевозки. На основании положительных результатов испытаний разрешено серийное восстановление авиашин с армированием протектора для эксплуатации на самолётах отечественного производства. Однако в начале 90х годов в общем потоке преобразований ЯШРЗ был ликвидирован, промышленное восстановление авиашин в России было прекращено.
На первом этапе ввода в действие вновь создаваемого производства восстановительного ремонта авиашин планируется освоение наиболее востребованных крупных шин для воздушных судов ИЛ-76, Ил-78, А-50, эксплуатируемых, как в ВВС и ВМФ, так и в ГА: шин 1300х480 1А основного шасси и 1100х330 26А – носового, к которым имелись претензии эксплуатационников (см. ниже).
При рекомендуемом сегодня 3х кратном допуске восстановления протектора вдвое сократится потребление авиапредприятием (АП) новых авиашин (таблица 1), доли восстановленных и новых шин в эксплуатации составят, соответственно, 60% и 40%, расходы на шины парка воздушных судов Ил-76, Ил-78, А-50 сократятся на 30%, экономия ~97 млн. руб. в год., а при освоении ремонта всего ассортимента шин, подлежащих восстановительному ремонту, ~288 млн. руб./г. Прибыль ШРЗ при принятом уровне рентабельности 15% составит ~20 млн. руб./год. Срок компенсации инвестиций – 2,5 года.
Во всех указанных расчётах принимается, что наработка шин, своевременно снимаемых с эксплуатации для восстановления, на 25% ниже наработки шин, эксплуатируемых сегодня с допустимым износом до корда каркаса, практически исключающим возможность их восстановления.
Экологическая эффективность восстановления шин определяется снижением загрязнения окружающей среды в результате сокращения темпов утилизации использованных авиашин и уменьшения вредных отходов производств, а также снижением расходов невозобновляемых материально-энергетических ресурсов страны. Расход материальных ресурсов снизится на 30%, ежегодная экономия невозобновляемых природных ресурсов – до 360 тн/год (таблица 1).
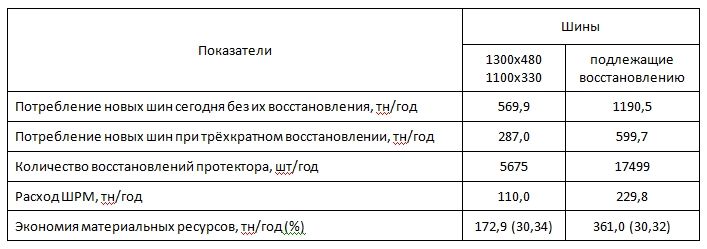
Одна из основных задач создаваемого производства восстановленных авиационных шин – улучшение их эксплуатационных качеств, в первую очередь исключение вибраций самолёта при взлёте, связанных с неоднородностью шин: их значительным дисбалансом, радиальным биением и неравномерной жесткостью вдоль окружности шины. Неоднородность новых шин возникает в основном вследствие недостаточной стабильности применяемых материалов, нарушения прецизионности сборки и вулканизации шины. Иногда имеют место даже запрессовки корда в крупные плечевые выступы рисунка протектора (рис. 1в). И как следствие – неравномерная разнашивамость шины в эксплуатации. А также вследствие неравномерного износа и деформации шины по эксплуатационным причинам, например, из-за нарушения норм нагрузки и давления в шине, нарушения углов установки колёс длительных статических нагрузок.
При восстановлении шин обрабатывают полностью разношенную, «стабилизированную заготовку», прошедшую во время доремонтной эксплуатации естественный отбор – отсев большинства шин с производственными дефектами, в т.ч. неоднородных. В процессе восстановительного ремонта могут быть успешно устранены указанные дефекты неоднородности шин.
Однако, применяемая традиционная технология механической обработки, сборки и вулканизации восстанавливаемых шин не решают эту задачу, а напротив, как правило, увеличивают неоднородность шины: на участках максимального биения шины в процессе срезки и шероховки остатков изношенного протектора удаляют максимальный слой резины, остаточная толщина стенки на этом участке короны шины минимальная, не редко сопровождается повреждением брекера. В результате в процессе восстановительного ремонта существенно увеличивается неоднородность, дисбаланс шины, ухудшаются её эксплуатационные качества. Возникают очаги повышенных напряжений, интенсивного теплообразования и разрушения шины.
Рисунок 2. Схема раздвижного барабана механизма посадки на жесткую опору восстанавливаемой шины по всей ее внутренней поверхности конструкции инженера Эпштейна М. Г. (Израиль):
А – механизм в рабочем положении;
Б – механизм в исходном сжатом положении;
В – положение сменных распорных колодок в сжатом состоянии;
Г – положение распорных колодок в разведенном рабочем состоянии;
1 – муфта; 2 – рычаги; 3 – распорные колодки; 4 – гайка; 5,10 – кожухи; 6 – несущая труба; 7 – опора; 8 – шпонка; 9 – винт.
Применение механизма посадки обрабатываемой шины на жёсткую опору с раздвижным барабаном (рис. 2) и затем обрезинивание каркаса шины прямым шприцеванием ремонтной резиновой смеси на подготовленную корону шины обеспечивают высокую прецизионность. Получаемая толщина стенки кроны каркаса при механической обработке шины определяется лишь расстоянием от рабочей поверхности раздвижного барабана до рабочей кромки фрезы шероховального станка, а при обрезинивании – расстоянием поверхности барабана до рабочей грани профилирующей планки литьевой головки экструдера. Обеспечивается точная регулировка толщины оставляемого старого подканавочного слоя без повреждения и оголения слоёв корда брекера и каркаса, в т.ч. и при удалении возобновляемых армирующих и защитных слоёв корда. А после обрезинивания обеспечивается требуемая стабильная суммарной толщины стенки короны вдоль всей окружности шины независимо от начального биения её каркаса.
Одновременно автоматически заполняются резиновой смесью все подготовленные к ремонту допустимые мелкие наружные повреждения каркаса. При этом обеспечивается максимальная плотность контакта и прочность связи без каких-либо захватов воздушных включений, характерных для других способов сборки. Резиновая смесь буквально «вмазывается» в шерохованный рельеф ремонтируемой поверхности. Исключается необходимость небезопасной операции нанесения клея на каркас восстанавливаемой шины. После обрезинивания проверяют дисбаланс каркаса и, если необходимо, устраняют его наложением в лёгкой зоне уравновешивающей массы тонкой ленты прослоечной резиновой смеси.
Затем взамен удалённых защитных и армирующих слоёв накладывают новые слои навивкой узкой ленты резиновой смеси, армированной нитью металлокорда либо одной, несколькими нитями нейлонового или другого высокопрочного текстильного корда.
Рисунок 3. Схема сборки шины с навивкой экранирующего слоя в окружном направлении:
1 – слои брекера;
2 – подканавочный слой протектора, навитый лентой резиновой смеси, армированной нитью металлокорда (в радиальных шинах) и одной или несколькими нитями высокопрочного текстильного корда (в шинах диагонального построения);
3 – протекторная резиновая смесь.
Экранирующий слой навит на брекерно-протекторном барабане узлом cap strip winder сборочного агрегата автомобильных шин VMI GROUP (Голландия).
Во избежание перегрузки и быстрого разрушения этих слоёв при работе шины в эксплуатации навивку обрезиненных нитей корда в окружном направлении осуществляют с применением специального устройства с расчётным натяжением на каркас, которому придают размеры по длине окружности, соответствующие его эксплуатационной форме. В результате, получают желаемую нагрузку навитого слоя во время работы шины в эксплуатации, обеспечивающую снижение напряжений в старых, утомлённых слоях брекера и каркаса и в то же время исключающую разрушение навитого слоя из-за его перегрузки. Испытания шин, выпущенных этим способом на экспериментальной установке НИИШПа с разгрузкой брекера на 25%, показали, что работа разрушения опытных восстановленных шин была на уровне новых, а прочность связи между слоями выше, чем у новых шин.
Заготовку с навитым экранирующим слоем вулканизуют в «гладкой» прессформе, не имеющей на рабочей поверхности гравировку рисунка протектора. При этом отсутствуют течения резиновой смеси, способные вызвать смещения навитых нитей корда, нити корда фиксируются в положении, строго заданном при сборке, и не изменяют его на следующем этапе производства. Затем накладывают на корону протекторную резиновую смесь, необходимую для формирования рисунка протектора методом Orbitread, который обеспечивает наиболее равномерное распределение наложенной на каркас смеси по всей окружности заготовки шины. Вулканизацию восстанавливаемой шины производят в вулканизаторе радиального типа, например, серии VRH AVIO компании ITALMATIC (Италия). Вулканизатор минимизирует возможность перераспределения резиновой смеси, наложенной на вулканизованный каркас, позволяет применять прогрессивные способы вулканизации: бездиафрагменный и зонный с дифференцированным температурным режимом по короне и боковинам, обеспечивающим снижение производственного брака, сокращение на четверть режима вулканизации и втрое расход теплоносителя – пара.
В результате изложенных особенностей технологического процесса предусматривается строгое соответствие восстановленных шин требованиям ТУ 38.404 276-94 на новые авиашины по габаритным размерам и массе, допуски статического дисбаланса Dcт устанавливаются на уровне Европейских стандартов «Федеральной авиационной администрации» (FАА) 2006 года (циркуляр FАА РЦ №: 145-4A, раздел 13 для восстановленных авиашин): 1100х330 – 3300 г.см., 1300х480 – 6300 г.см., которые существенно (в 5-6 раз) ниже норм ТУ на новые отечественные авиашины. Соответственно, снижаются колебания вертикальной силы в пятне контакта авиашин (Δ F) (таблица 2) ΔF=2(Dст) Ω2, где Ω – максимально допустимая угловая скорость шины. Ожидаемое снижение уровня колебания вертикальной силы в пятне контакта авиашин с взлётно-посадочной полосой, показанное в таблице 2, практически исключает вибрации, мешающие управлению самолётом.
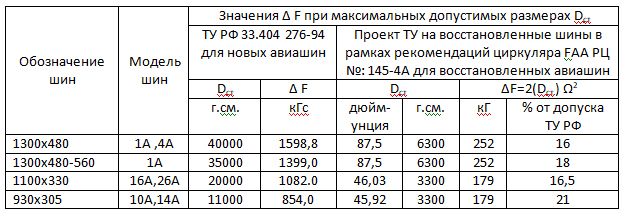
Резюме
1. Грамотная эксплуатация авиационных шин с их своевременным восстановительным ремонтом при допуске трёхкратного возобновления изношенного протектора позволит: вдвое сократить потребление новых авиашин, на 30% снизить затраты авиационных предприятий на шины. При этом в эксплуатации доли новых и восстановленных шин составят, соответственно, 40% и 60%.
Экономия, получаемая от восстановления только шин первой очереди 1300х480 и 1100х330, составит ~ 100 млн. руб. в год. При освоении восстановительного ремонта всего ассортимента авиашин, подлежащих восстановлению, снижение затрат авиапредприятий на шины составит более четверти млрд. руб./год., прибыль предприятия по восстановлению авиашин составит ~ 20 млн. руб./год. Окупаемость капиталовложений инвесторов — 2,5 года. По меньшей мере вдвое снизится импортозависимость гражданской авиации страны.
Реализация изложенных мер позволит существенно улучшить эксплуатационные качества шин, в т.ч. исключить вибрации, связанные с неоднородностью шин, наряду с тем, что послеремонтная наработка восстановленных шин и их безопасность обеспечиваются на уровне новых шин.
Заметно повысится экологическая безопасность: вдвое уменьшится загрязнение окружающей среды, на 30% сократится расход невозобновляемых материально-энергетических ресурсов страны.
2. Непременное условие достижения этих результатов
Грамотная эксплуатация авиационных шин, выполнение элементарных правил, в т.ч.: соблюдение норм внутреннего давления и нагрузки, углов установки развала и схода колёс, износ протектора до индикаторов износа его рисунка (или при их отсутствии только на глубину рисунка), обязательное снятие с эксплуатации шин, пригодных для восстановления, не допуская износа их до каркаса, как принято сегодня, регулярная чистка аэродромного покрытия от посторонних колющих, режущих предметов, не допускать в обычной практике агрессивных методов эксплуатации шин и т.п.
3. В настоящее время ОАО «Меларис» ведёт строительно-монтажные работы по созданию в Московской области современного производства восстановленных авиационных шин. Для завершения этих работ, доукомплектования приобретенного оборудования, выполнения пусконаладочных работ и квалификационных испытаний головных партий восстановленных авиашин (в т.ч. лётных) ОАО «Меларис» нуждается в поддержке. в размере ~150 млн. руб.
В нынешней политической ситуации укрепления связей с Китайской народной республикой [1,2] представляется весьма актуальной участие КНР в поддержке указанной работы ОАО «Меларис», в т.ч. в создании упомянутых в этом обзоре узлов подготовительно-сборочного оборудования восстановления авиашин, в противовес санкциям, особенно в свете реализации недавнего визита председателя КНР Си Цзыньпина.
1. ТВ Россия 1, Программа «Москва, Кремль Путин». К 100-летию гражданской авиации РФ. 12.02 2023г.; к визиту председателя КНР Си Цзыньпина 22.03.2023 г.
2. Журнал «Дыхание Китая», март 2023 г. №2.
Авторы:
- Евзович В.Е. — к.т.н., чл.-корр. Общественной академии Проблем качества РФ.
- Мухин А.Ю. — генеральный директор ОАО «Меларис».
- Шехтер В.Е. — консультант по технологии производства шин ОАО «Меларис»